Corrosion Prevention: Anodes, Nail-polish, and Continuity Checks
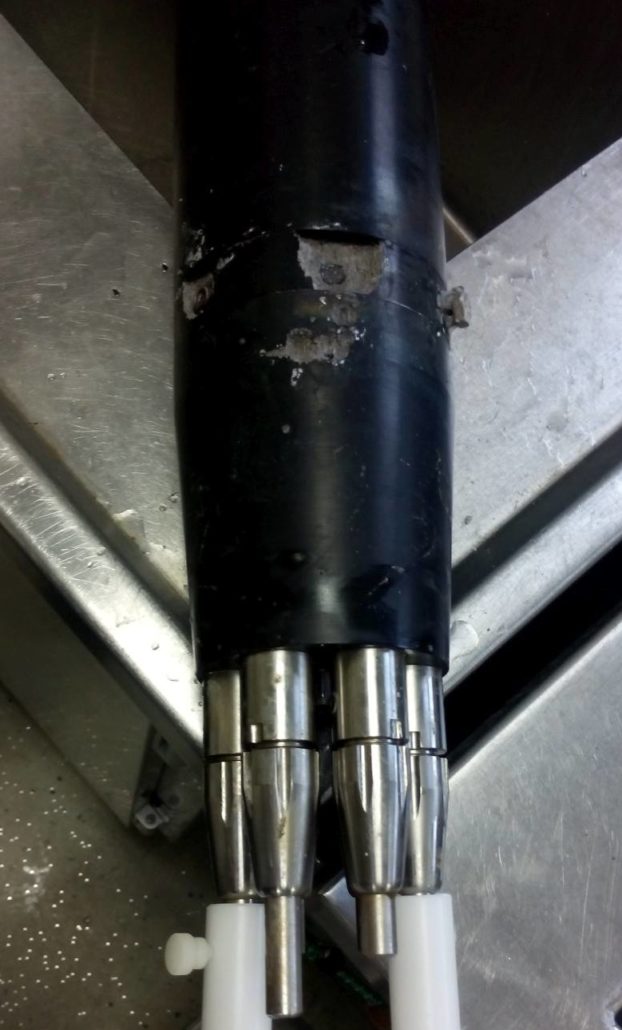
Extreme corrosion on a MicroRider-1000 after a long-term deployment with zinc anodes
Corrosion prevention is an easy to overlook, yet critical practice for operating in the corrosive environment of the ocean. Your Rockland Scientific MicroStructure instrument is equipped with one or more sacrificial anodes to prevent corrosion of your instrument. The anodes are electrically connected to the entire instrument providing protection to the instrument when submerged in seawater.
It is important to note that anode protection only works while the instrument is submerged in seawater. When the instrument is in air, the anodes stop working and any residual sea water will cause corrosion to occur at vulnerable sites. For this reason, it is important to thoroughly rinse the instrument with fresh water, especially when it is not active for more than 24 hours. Before storing the instrument, it is imperative that the instrument is completely dried, as even fresh water (or dampness) can lead to corrosion if left long enough.
Zinc Anode vs. Aluminum Anode
In 2015 Rockland Scientific’s Production Tech John Wells conducted an internal study of corrosion affecting Rockland MicroStructure instruments. The key findings of the study are:
- Aluminum anodes (mil spec. MIL-A-24779) provide superior protection and longevity than zinc anodes
- Over time zinc anodes build a layer of oxidation that can insulate the anode from seawater diminishing its effectiveness
- Aluminum anodes are formulated to slough off any oxidation resulting in continued peak performance.
- Placing a rubber washer under the anode helps prevent seawater from oxidizing the threads of the anode screw, thereby ensuring a good electrical connection.
The study findings greatly enhanced the understanding of corrosion prevention at Rockland Scientific. If you have an instrument with an original zinc anode please ensure that the zinc is well scraped off before each deployment. Not all aluminum anodes are created equal, the study determined that a particular anode alloy formulation works best. Rockland recommends that customers source their own spare aluminum anodes with mil spec: MIL-A-24779. If you would like an aluminum anode to replace a zinc anode on your instrument please contact technical support to request a complimentary aluminum anode and rubber washer.
Copper tab connecting the rear bulkhead to pressure tube
Consider the anode on the rear bulkhead of a VMP-250. The anode is electrically connected to the rear bulkhead by the threads of its mounting screw. The copper tab on the rear bulkhead contacts the inside of the pressure tube where the anodized layer has been intentionally removed. It is important to check that the copper tab is making a connection to the pressure tube. Overtime the copper tab can become bent and oxidized. The oxidization can easily be removed with sandpaper. You should hear and feel the tab making contact with the tube when the rear bulkhead is inserted into the tube. If you do not hear and feel the tab making contact then gently bend it back into place. You can test if the copper tab is effective by performing the continuity check described below.
Continuity Check
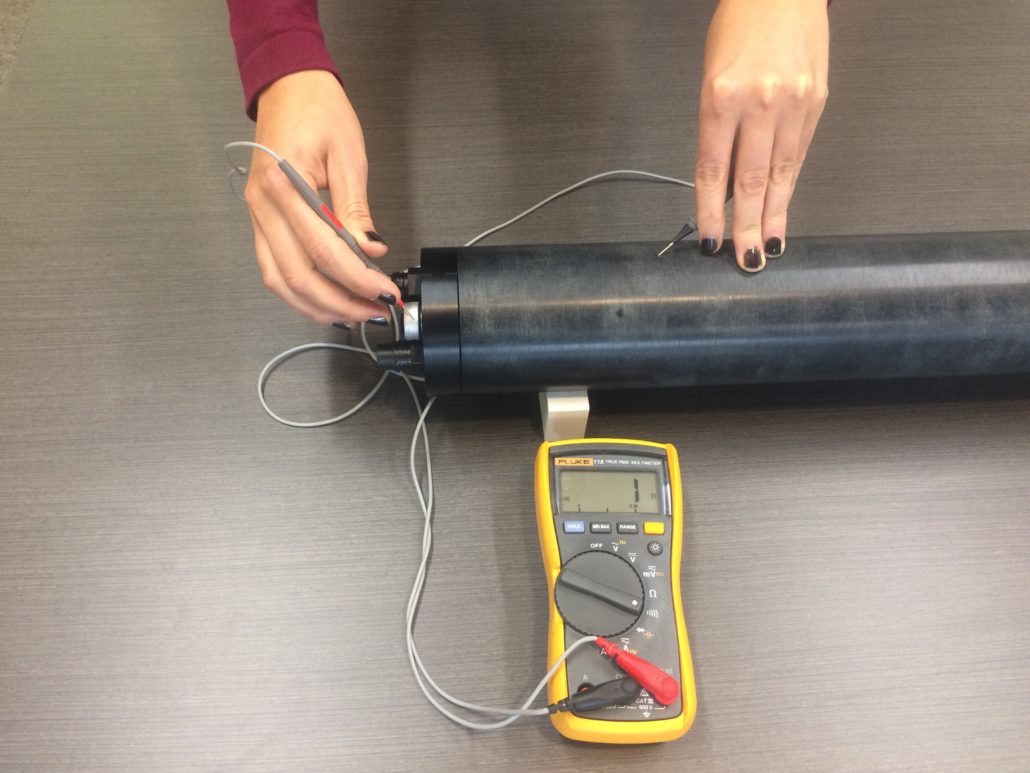
Checking the continuity between the rear bulkhead anode and a scratch on the pressure tube of a MicroRider-1000
Before you deploy your instrument, you can confirm the anode will do it job by performing a continuity check. Use a digital multimeter on the continuity (beep) setting and test for continuity between the anode and any exposed metal such as the rear sealing nut, the front sealing nut, any scratches in the black anodized layer and the connectors on the rear bulkhead. If there is electrical continuity between these parts and the anode then the anode will help protect them from corrosion.
Nail-polish
It is helpful to have two purposes for everything you bring with you to sea. In addition to making you look your best on deck, nail-polish is effective as a paint to cover nicks and scratches on your instrument. The pressure tube has a black anodized layer that electrically insulates your instrument from seawater. This insulation helps prevent corrosion of your instrument. When the anodized layer is broken, for example from being scratched by sharp fingernails, the exposed metal will start to corrode. To prevent corrosion of exposed metal, thoroughly wash, and dry off, the damaged spot and surrounding area, then paint over with nail-polish. Black nail-polish is often used for aesthetic reasons, but many users prefer a clear polish to allow periodic monitoring of the site.
Freshwater
Please note that while fresh water is much less corrosive than seawater, proper corrosion prevention practices should still be followed when operating in freshwater bodies. Aluminum anodes will remain effective in freshwater, however for long-term deployments in freshwater Rockland recommends magnesium anodes. Please contact Rockland if you would like to discuss the best option for your application.
Maintenance Tips Review
- Rinse instrument with freshwater after each deployment
- Ensure instrument is dry before storing for more than 24hours. Remember, corrosion never sleeps!
- Perform post cruise maintenance and cleaning before long-term storage
- Check electrical continuity between anode and sealing nuts and any scratches on pressure tube
- Bend and sand copper tab on rear bulkhead if necessary
- Paint any exposed metal due to scratching with nail-polish
- Scrape oxidization off zinc anodes before each deployment
- If you have a zinc anode please request a replacement aluminum anode from Rockland
- Clean the anode bolt and coat threads with anti-seize lubricant such as Never-Seez to ensure continuity between rear bulkhead and anode
- Magnesium anodes are recommended for long-term freshwater deployments